- The next website linking is only available in Chinese.
- If you have any questions, please dial +886-2-2311-2031.
Continue to the website.
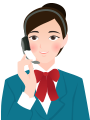
2024-09-30
Like a Slice of Pizza: TSMC Strikes Gold with New CoWoS Packaging Technology
The long-awaited big break in 3D integrated circuit (IC) packaging, which has finally come to pass in the age of AI, has been more than ten years in the making. Since its debut at SEMICON over a decade ago, when it took the semiconductor packaging sector by storm, TSMC’s CoWoS 3D packaging business has grown 60% every year. Now it is threatening to overtake the ASE Group and become the industry leader. What made TSMC Founder Morris Chang decide to buck the odds and compete in IC packaging? This column was published during SEMICON Taiwan 2024, the annual extravaganza for the global semiconductor industry. Technology leaders from around the world jetted in just to take part in the various forums held around Nangang Exhibition Center. Related discourses cover the latest trends, such as silicon photonics. The results of these dialogues could have a lasting impact on the semiconductor industry. TSMC’s CoWoS IC packaging technology, the revolutionary breakthrough in semiconductor manufacturing that’s the darling of Taiwan’s stock exchange, debuted at SEMICON 13 years ago. At the time, all that anyone in the field could talk about was “3D IC”. The idea was to pack multiple dies side-by-side on the silicon interposer at the wafer level to greatly enhance interconnect density and reduce chip footprint. Other industry giants such as the ASE Group and Siliconware Precision Industries Co. (SPIL) were champing at the bit to get in on the ground floor. Then a senior director from TSMC dropped a bombshell: TSMC was entering the 3D IC business, offering a simplified version of the advanced packaging technology to its clients. The thousand representatives of IC packaging companies were in agony. “Are you saying we are all out of a job?” the vice president of research and development at a major company asked in distress. During TSMC’s shareholders’ meeting a month later, Morris Chang (張忠謀) officially announced that TSMC was introducing its CoWoS “chip-on-wafer-on-substrate” technology. Like a middle school English teacher, Chang made sure that everyone pronounced the name correctly. Turning Mistakes into Miracles The rumor was that the backlash from the packaging industry was so fierce that Chang had to make a personal announcement to soothe the controversy and make it clear that he stood behind his company’s decision. The senior director who kicked things off was none other than Dr. Douglas Yu (余振華), Vice President of Pathfinding for System Integration at TSMC, who has recently been awarded a fellowship at Academia Sinica. He was the pioneer behind two of TSMC’s most groundbreaking technologies: CoWoS, which is used in high-performance computing, and InFO, which is used on mobile devices. The former is the darling of Nvidia’s GPUs; the latter is used in Apple’s self-developed computer chips. This was a whole new wellspring of revenue for TSMC. In his announcement, Chang declared the reason that TSMC was getting into the packaging business was to create “a clear ownership of [the] long process flow”. This reporter did not quite understand the explanation until years later. At its core, the question boils down to “who should pay—and how much should they pay—when something breaks?” Take Nvidia’s AI accelerator, the H100 GPU, as an example. If its architecture was a slice of Hawaiian pizza, the ham on top would be the 4-nanometer GPU chips, and the pineapple pieces would be High Bandwidth Memory (HBM). The cheese below would be the silicon interposer, which rests atop the dough—the IC substrate. When packaging companies talk about working with 3D IC, think of it as TSMC making the “ham” and selling it to ASE or SPIL, who then buy the “pineapple” from SK Hynix Semiconductor to combine everything into a slice of pizza. A packaged H100 chip costs over US$30,000. Just the “ham” made by TSMC costs a few thousand dollars. Packaging companies face a harsh reality. The “cheese” in the middle, the silicon interposer, requires wafer-level manufacturing expertise. It is extremely difficult. Failure would mean that the expensive “ham” on top would be kaput as well. Herein lies the point of contention. TSMC’s profit margin is over 50%, which means its “ham” has a price tag that’s double the cost. But if TSMC did the packaging itself, the cost of failure would not include the lucrative profit margin. “If they break it, they buy it. But if I break it, I have to pay twice as much. Of course it’s hard to compete,” Mike Ma (馬光華), the former vice president of research and development at SPIL who single-handedly built its advanced manufacturing line, explained the dilemma to this reporter some years ago. Even if packaging companies quoted the lowest price possible, they still couldn’t compete. Ultimately, this led to TSMC monopolizing the field of advanced IC packaging. New Hope for IC Packaging The big break in 3D IC, which the packaging segment of the semiconductor supply chain has waited for all these years, is finally on the cusp of realization thanks to generative AI. The manufacturing of the H100 chips has been limited by the production capacity of CoWoS. TSMC has agreed to give some of its orders to ASE and the American company Amkor Technology. However, this is restricted to the latter half of the CoWoS process. In other words, it’s the final phase when all the toppings are placed on the “dough”, or the IC substrate. Industry veterans point out that TSMC has already accrued over a decade of mass production experience. “They are taking it easy because they are so far ahead.” But they also stipulate that contactors replicate TSMC’s process with zero variation, down to the equipment, materials, and production parameters. The substantially more challenging first half the process, “chip-on-wafer”, may also be outsourced to suppliers. ASE is gearing up for this once-in-a-lifetime opportunity. This is why its expenditure this year is a record-shattering US$3 billion. TSMC Chairman Dr. C.C. Wei (魏哲家) introduced a strategy he dubbed “Foundry 2.0” this July. The plan: expand the definition of wafer foundry to officially encompass packaging and testing. He feels that this new definition will offer a new shot at growth for TSMC. How big of a chance is it? For CoWoS, TSMC is projecting a CAGR of up to 60% between 2022 and 2026. Advanced packaging is just 10% of TSMC’s business. In a few years, if things move quickly, it could overtake ASE to become the world’s largest IC packaging company. During the 2024 Technology Symposium, TSMC unveiled a new iteration of CoWoS called “system-on-wafer”, or SoW. It can produce a massive chip that’s about the size of a 12-inch wafer. These products will be used in a new generation of data centers. It shows just how far TSMC’s technological dominance has come. In the past, chips were in a race to downsize. But due to demand from customers in the AI industry like Nvidia, a paradigm shift has occurred where the packaging process will churn out larger chips. Wei has admitted that TSMC is also branching out into panel-level packaging, where chip size is even less of a limitation. At the earliest, the new products will launch in three years. We should not be surprised if Nvidia CEO Jensen Huang (黃仁勳) wows the crowd with new AI chips that are the size of table tops.
2024-07-31
AI Foundries Offer Taiwan a Good Chance to Replicate TSMC’s Success
Taiwanese companies are currently profiting from the first wave of the AI revolution, but where will the next source of growth come from? Even Nvidia CEO Jensen Huang is exhorting the virtues of AI foundries—a system under which the creation of AI models is outsourced to contractors. This may give Taiwan’s AI supply chain a substantial competitive edge. In an exclusive interview with CommonWealth Magazine, Dr. Liang-Gee Chen (陳良基), Professor Emeritus of the Department of Electrical Engineering at National Taiwan University, posits that if Taiwan can leverage its advantages in hardware and software integration, it can become the island kingdom of the world’s most trusted AI foundries. Artificial intelligence (AI) is the latest iteration of the industrial revolution. At this moment, tech giants like Microsoft, Meta, and Google are competing over what is the most profitable way to work with hardware suppliers. In the semiconductor industry, on one end of the spectrum are “integrated device manufacturers”, or “IDMs”, represented by Intel. On the other end are companies like TSMC, which exemplify a more open approach to operating wafer foundries, one that revolves around specialization and division of labor. With regard to the tech industry, Taiwan’s decision to divide the work among different companies on the supply chain birthed an incredibly strong semiconductor sector. It also nurtured our hardware integration capabilities, which is why so many functions are now integrated into the microchips we make. In the age of AI, when everyone is using AI to do more than was previously possible, the question we should ask is: Who will be the supplier of AI? Current AI suppliers that appear to be far ahead of the competition are like chip suppliers in the early days of the semiconductor boom, such as Intel 40 years ago. What really infuses AI with new abilities is the data on which it is trained. If all our data is in the hands of the aforementioned tech leaders, like Microsoft, Google, and Amazon Web Services (AWS), then they themselves will become the new generation of IDMs, as users will rely on the AI models that they provide. Two years ago, I was already promoting the concept of the “AI Foundry”. I use the word “foundry” to convey the meaning that, no matter where the user is located, they can trust the AI that Taiwan provides. This is because in the age of AI, people are not as worried about computing power as they are about data. If we’ve already done the computing for you and given you a fine-tuned AI model, computing power becomes a less critical part of the equation. If this is where the AI industry is headed, then whoever becomes a trusted contractor that can take on outsourced AI workloads will become the most important supplier in the entire AI industry. To use the semiconductor industry as a familiar example, microchips make up the core of servers, while cloud service providers (CSPs) and computing providers form the second link in the supply chain. The final link comes from service providers who create AI models, such as OpenAI. Taiwan’s chance lies in this final link of AI model services. Taiwan can offer the world an open environment where users of AI models don’t need to surrender their data to a monolithic IDM. Instead, they can outsource the training and fine-tuning of their AI models, just as they did with microchips. It goes without saying that the contractor must be able to be trusted not to leak precious and sensitive data. Taiwan Unrivaled in OEM/ODM Taiwanese companies have made a name for themselves on the world stage because they are unrivaled when it comes to OEM and ODM—outsourced contracting work. The world trusts that the job will get done if it is in the hands of a Taiwanese company. Therefore, it won’t take long for international clients to get used to a new model in which data is delivered to Taiwanese vendors for AI development. The clients control their own data and can make adjustments as they see fit. They are not restricted by the rules of existing IDMs, i.e. “If GPT4.0 is what’s available, that’s what you're using; if there’s an update, then you’d better get on-board.” Nowadays, if a company wishes to use AI, it must hand over its data to OpenAI for training. In the end, OpenAI controls all the information. But is OpenAI’s business model trustworthy? TSMC is trusted because it doesn’t compete with its customers. Will OpenAI compete with its customers? Right now, there’s no way to know. How OpenAI fine-tunes its data is also a huge unknown. The whole thing is very different from the semiconductor industry. With semiconductors, when you outsource to TSMC, not only are you certain that it will not compete with you, you can also tell TSMC what design you want as well as what you want to adjust. Everything that is discussed is confidential and will not be released to the public. But when you give your data to OpenAI, you are in fact helping them to train their AI models. OpenAI owns all of your data. For this reason, many big companies prohibit their employees from using AI services from OpenAI. What Customers Need is a Business Model Where They Control their Data Hence, the common pain point of enterprises is this: Is there an unrestricted AI development tool that can be controlled by the user? This is a chance for Taiwan to demonstrate its strengths. We already have the hardware, and the quality of our work is universally trusted. We can leverage that trust to invite enterprises to let us work with their data and develop the perfect AI model for them to use. In a future where every profession is using AI, it is imperative for AI suppliers to allow their users to exert tighter control over their data and enjoy absolute peace of mind. OpenAI is a closed system; users may only need a smaller model to get the job done. For example, a user who requires art design services does not need the AI to also know how to write poems. If we can get a clearer picture ahead of time of what sort of know-how and knowledge are required, we will be able to tell when a smaller AI model will suffice, which cuts down on the amount of computing resources that are needed. In many ways, Apple is already headed in this direction. Taiwan controls the microchips at the heart of AI hardware. Therefore, if we know what customers are looking for, we can simplify the workload for them, to the point that we may even be able to recommend more cost-effective hardware configurations. In summary, the “AI foundry” service needs both hardware and software integration. In all the world, no one does this better than Taiwan. A time will come when every industry needs more independent AI models. The IDMs of the current AI wave will face many challenges in the future, just as Intel had to learn how to outsource its manufacturing. This is because the current AI models are trained in a grab bag, one-size-fits-all fashion. It will not be easy for AI developers who built their success on this foundation to adapt to training smaller AI models. In the end, it all comes down to who controls the data, because that's where the money is. For example, TSMC has remarkable production prowess mainly because it adopted smart manufacturing early on. Smart manufacturing has already become mainstream; there are probably over 30 fully automated factories in Taiwan. This was made possible by collecting data and then using it to manage the factories. All the manufacturing know-how is in the data. That is why it is so important to control the data: It is a competitive advantage. Taiwan Can Invest in Open-source AI Models Taiwan can help train the world’s open-source AI models. That is why we are currently working with Lama3. When it comes to training AI models, Taiwan can work with anyone on Earth who is willing to provide open-source AI models. We can elevate this market; with Taiwan’s help, this can become our edge when competing with the IDMs of the AI world. The current IDMs have everything going for them, and if they invest in things that solve their customers’ pain points, they may continue to dominate the market. If Taiwan can put its full strength behind the plan outlined above, just as we did for the semiconductor industry, and if our policymakers can take into account Taiwan’s role in the supply chain of the world’s AI foundries—then Taiwan will have a greater chance to thrive in the age of AI. Read the full article in CommonWealth Magazine.
2024-06-28
A Brief Summary of the Advantages and Challenges of Developing Compound Semiconductors
Due to their use in Tesla's Model 3, compound semiconductors, also called "third-generation semiconductors" or "Group III semiconductors", briefly became the hottest topic in the global tech sector. In recent years, another nascent industry besides electric vehicles that may offer new business opportunities for compound semiconductors has appeared: AI servers. In the era of AI, deploying compound semiconductors to improve power usage effectiveness is of great importance. But what difficulties and challenges are faced by the compound semiconductors sector in terms of materials, production, and application? Below are the latest insights from Dr. Yi-Jen Chan (詹益仁), former CTO of the Delta Group's Cyntec Co., former General Director of the Electronics and Optoelectronics Research Laboratories at the Industry Technology Research Institute (ITRI), as well as a founding father of the compound semiconductor industry. Compound semiconductors benefit from the attributes of groundbreaking materials such as gallium nitride (GaN) and silicon carbide (SiC), allowing them to be smaller, lighter, and recharged more quickly. This field took off with electric vehicles (EVs), but recently there has been more bad news than good from the EV world as the market enters its corrective phase. Fortunately, compound semiconductors have found a new wealth of opportunities with the rise of servers used for artificial intelligence (AI). During a shareholders' meeting last year, the chairman of Delta Electronics announced that their newest 3,200W 80 PLUS Titanium server power supply utilizes components made from GaN to drastically increase energy density by 25% and improve energy efficiency from 94% to 96%. The Difference Between a 2-lane and a 10-lane Highway High power consumption is a major headache for generative AI. AMD CEO Lisa Su has said that in several more years, a supercomputer might have to be powered by a nuclear reactor. Research has shown that by 2027, AI will use as much energy as the entire nation of the Netherlands. The advent of AI means that both CPUs and GPUs will consume more and more direct current (DC) power. What was once 200-300W is now 700W, and one day it could be 1,000W or even 1,500W. Such high energy demands will have to be satisfied with power semiconductor devices. Technical Requirements of AI Applications Will Be Different from EVs Because the voltage requirements of CPU and GPU chips are actually low—around 0.7V—power supply units need to take 12V or 48V currents and convert them to 12V, 5V, or even 0.7V. These conversions are done through semiconductors. When it comes to working with electric currents, power semiconductor devices made from GaN have advantages over silicon-based semiconductors. To begin with, silicon-based semiconductors can be compared to two-lane highways; too many cars on them will slow the traffic down and decrease performance. In comparison, GaN-based semiconductors are like ten-lane highways that allow for 100-mph driving even in heavy traffic. As current drivers for CPUs and GPUs, they offer better performance due to lower electrical resistivity and a higher conversion rate. The second advantage concerns how the transistors turn on and off during power conversion. On a GaN chip, turning off one control valve stops all traffic. Because it switches very quickly, it can use much smaller passive components. A silicon chip, however, requires a primary valve and many supporting valves. All of these must be shut off to stop the flow, complicating operations. Complications in Production Relegate These Chips to Niche Markets And yet, over the last 30 years, silicon-based semiconductors progressed by leaps and bounds while compound semiconductors treaded water. This is because they were relegated to niche markets such as defense and aerospace. Mass adoption by the commercial market has been slow in coming. The transistors of compound semiconductors have more irregularities than silicon chips, with many minute disparities that are harder to control. The material itself is hard to work with, and the production process is beset with difficulties. This is because the compound is made of two or three different materials that react differently to temperature changes and vaporize at disparate speeds. More importantly, the compound doesn't have a stable layer of oxygenation like silicon chips. This limits its viability in commercial use and pigeonholes it as a futuristic substance that may see broader adoption—one day. It wasn’t until power amplifiers (PA) were widely used by third-generation communications equipment that compound semiconductors shook off their ten-plus years of inactivity and basked in the spotlight once again. Will Compound Semiconductors Create a New TSMC? Whether compound semiconductors can give rise to a new TSMC depends on the economy of scale. Silicon-based semiconductors have the scale to support a vertical supply chain in Taiwan. However, compound semiconductors have long been the products of a niche market. It would not be feasible to try and replicate the same business model in this market; vertical integration would be a necessity. This is the biggest difference between compound semiconductors and silicon-based semiconductors. Like the SiC chips that Tesla developed for years in its lab before putting them in the Model 3, many of the considerations come down to business strategy. The economy of scale determines the choice of components. Not everything in this supply chain can be divided into vertical slices. Silicon-based chips have withstood the test of the mass market and inspired many new inventions, from the smartphone to the currently trending AI. From 28 nanometers to 15, 10, and 5 nm, they all have their uses. Tech innovation is driven by actual demand. Compound semiconductors have thrived in a niche market. They don't have a guiding principle like the famous Moore's law, and neither do they have the resources of the entire world focused on solving a common problem. On top of the difficulties of working with the materials, it might also be said that Tesla was only able to put SiC chips in its cars because it was operating like a startup eager to buck the trend. SiC chips are more expensive than mainstream alternatives. Despite this disadvantage, from the perspective of the entire system, if these pricier components can solve the issue of heat dissipation, they may be a worthwhile investment. Tesla's use of compound semiconductors was an important first victory. In business, no one wants to be the lab rat. There is a certain psychological barrier to adopting new technology. But SiC is a proven and reliable material for making semiconductors. Once a first mover has tried using it, and all the cars outfitted with SiC semiconductors turned out to be perfectly functional, more people will get on board. China is Catching Up: BYD is Also Getting in on the Action After Tesla set the precedent for working with SiC, China's BYD also got in on the action. Everyone knows that BYD uses Chinese technology for the Chinese market, so people are wondering: If the future of SiC is tied to the EV industry, and if BYD makes its own chips and cars, then what future is there for Taiwan's SiC companies? "Third-generation semiconductors" is actually a term that came out of China. Chinese firms are heavily invested in it, the whole ecosystem is getting more and more complex, and many big companies around the world are already signing long-term contracts with them. Chinese companies use low prices as their competitive strategy. Right now, we don't know what Taiwan's strategy is. What we do know is that we cannot use the same strategy as that of silicon semiconductors. What Taiwan needs is more vertical integration. For example, packaging can get involved in material production. There are many technologies that can be combined. If we can do a good job with integration, we will still have opportunities.
2024-05-09
Taiwan launches chip-based industrial innovation office
Vice Premier Cheng Wen-tsan (center) is joined by National Science and Technology Council Minister Wu Tsung-tsong (second left), other officials and business representatives in opening an office to promote the Taiwan Chip-based Industrial Innovation Program May 7 in Taipei City. (Courtesy of NSTC) An office to promote the Taiwan Chip-based Industrial Innovation Program was launched by the National Science and Technology Council May 7 in Taipei City, highlighting government intentions to advance technical prowess over the next decade. Approved by the Executive Yuan last year, the program will receive government funding of a total NT$300 billion (US$9.25 billion) between 2024 and 2033. It focuses on four areas: integrating generative artificial intelligence with chip manufacturing; improving personnel cultivation; accelerating breakthroughs in innovation technologies such as the IC design; and attracting international startups and investment. According to the NSTC, the office’s tasks include observing and analyzing major countries' and international manufacturers’ semiconductor operations. It will conduct research and analysis on the four major areas above and provide recommendations to adjust overall strategic planning on a rolling basis. Speaking at the opening ceremony, Vice Premier Cheng Wen-tsan said that the program will boost Taiwan’s technology by driving innovation in various sectors via generative AI and semiconductor applications. He added that the office will further serve as a platform for cooperation among ministries, academic institutions and businesses while securing Taiwan’s strength on the global semiconductor stage. Following Cheng’s remarks, NSTC Minister Wu Tsung-tsong expressed similar sentiments, and said that the office will note domestic and international trends while adjusting relevant implementations to make Taiwan a global model for industrial innovation. The NSTC added that a public-private alliance is also in the pipeline to integrate resources and strengthen the development of the country’s industrial ecosystem. (YCH-E) Write to Taiwan Today at [email protected]
2024-02-29
Japan’s Semiconductor Equipment Industry Policies and Guidelines
I. Introduction Japan actively developed its semiconductor industry in the 1970s, creating a complete industrial chain with outstanding performance in manufacturing, materials, equipment, and terminal products. At one point, Japanese semiconductors exceeded 50% global market share. But since the U.S.-Japan Semiconductor Agreement of 1986, Japan's market position has gradually fallen behind Taiwan and South Korea, with the current global market share sitting at less than 10%. In recent years however, Japan has been actively developing its semiconductor industry chain. Measures include encouraging foreign investments from companies like TSMC and Micron, as well as establishing Rapidus, which aims to mass-produce the most advanced logic chips smaller than 2 nanometers by 2027, to expand the global market share of Japanese chips to 20% by 2030. While Japan may still need to catch up in logic IC manufacturing, it is still the world leader in semiconductor materials and equipment, representing about 50% and 30% of the global market respectively. II. Japan’s world-leading semiconductor equipment industry The global semiconductor equipment market is primarily dominated by the United States, Japan, and the Netherlands. Among the top 10 equipment manufacturers, the United States accounts for about half of the market share, followed by Japan and the Netherlands, accounting for 30% and 20% respectively. Japan exports most of the semiconductor equipment it manufactures. In 2022 alone, Japan had US$8.35 billion in domestic demand for equipment, accounting for 7.8% of the global market. However, equipment exports were significantly higher, amounting to 4.3 trillion JPY (approx. US$28.5 billion), with about 23.8% (approx. US$6.78 billion) exported to Taiwan. Semiconductor production equipment constitutes the majority of Japan's semiconductor equipment exports, accounting for nearly 60% of total exports, followed by components at about 20%. In terms of manufacturers, Japan's largest semiconductor equipment manufacturer is TEL (Tokyo Electron), also the third-largest equipment manufacturer in the world. Other Japanese manufacturers in the top ten worldwide include Advantest, SCREEN, and Hitachi High-Tech. In the equipment category, Japanese coating/developing equipment (mainly TEL) accounts for more than 80% of the global market. Additionally, Japanese DUV (deep ultraviolet) photolithography machines, vertical CVD (chemical vapor deposition) and oxidation diffusion equipment, sputtering equipment, CMP (chemical-mechanical polishing) equipment and factory handling equipment also occupy important position in the industry. Ⅲ. The future layout of Japan’s semiconductor equipment industry The COVID-19 pandemic has underscored the importance of digital transformation. Japan's Ministry of Economy, Trade and Industry released its first Strategy for Semiconductors and the Digital Industry in March 2021. This strategy highlights the urgent need for advancements in semiconductor technology, manufacturing, and digital infrastructure, aiming to address the technological requirements for future trade and economic security. It sets a goal for Japanese semiconductor companies to increase their revenue from 5 trillion JPY in 2020 to 15 trillion JPY by 2030, ensuring a stable domestic supply of semiconductors. The strategy focuses on five areas: advanced logic ICs, advanced memory, industrial use semiconductors, advanced packaging, and manufacturing equipment and components/materials. It is estimated that by 2030, the public and private sector investments in advanced semiconductors and their supply chains will exceed 5 trillion JPY. Additionally, Japan aims to strengthen its domestic semiconductor equipment manufacturing supply chain and develop equipment for of next-generation technology, including advanced and green manufacturing equipment. The Economic Security Promotion Act also guarantees subsidies for operators whose equipment investment exceeds 30 billion JPY, which will enhance supply chain resilience and domestic manufacturing capabilities. To improve its self-sufficiency in advanced semiconductor manufacturing, Japan has initiated infrastructure projects in various prefectures, including a TSMC’s logic IC factory in Kumamoto, a Flash-3D NAND factory in Mie Prefecture (a joint venture between Kioxia and Western Digital), and a Micron’s 1β generation DRAM factory in Hiroshima Prefecture. Notably, TSMC’s Kumamoto fab, with an investment of US$8.6 billion, is a key development in advancing industrial-use semiconductors in the Kyushu region. This initiative is expected to generate 4.3 trillion JPY in economic benefits for the area over the next decade and has spurred other companies to establish factories in Kumamoto. Furthermore, since the establishment of JASM at the end of 2021, at least 46 semiconductor-related manufacturers to make new investments in the Kyushu region, promoting local economic development and enhancing Japan's competitive position in advanced semiconductor manufacturing. In recent years, Japan has actively collaborated with governments and enterprises from various countries to enhance the resilience of its semiconductor supply chain and bridge the gap in advanced technology fields. The Japan-U.S. Summit Meeting of 2022 established the Basic Principles on Semiconductor Cooperation, wherein the two nations committed to jointly bolstering supply chain resilience within the free trade market and supporting each other in addressing shortfalls in semiconductor manufacturing, manpower, technology and semiconductors. Japan has also formed a semiconductor partnership with the United Kingdom and held an Exchange of Views with senior executives of global semiconductor companies. Additionally, Japan's Ministry of Economy, Trade and Industry announced the resumption of semiconductor material exports to South Korea, ending a trade dispute that lasted three years and nine months. Despite these developments, Japanese semiconductor equipment manufacturers remain cautious above moving production capacity overseas, mainly due to considerations of geographical location and preventing technology outflow. In line with the New Export Controls on Semiconductor Equipment announced in March 2023, Japan, similar to the US, will impose controls on semiconductor equipment that may be diverted for military purposes. However, countries on Japan's list of friendly countries, including the United States, Taiwan, South Korea, and Singapore, are exempt from this restriction. Ⅳ. Complementary strengths: Taiwan and Japan working together to build up supply chain resilience Post COVID-19, Japan and other countries around the world are actively developing their local supply chains. Although Japan's semiconductor production capacity may have decreased from its previous heights, the country still holds a leading position globally in terms of equipment and materials. In recent years, Japan has actively cooperated with overseas companies in the semiconductor industry. However, due to concerns of national security and potential technology outflow, Japan remains selective in its partnerships. One such company, JASM, a joint venture with TSMC, which plays a crucial role in filling the gap in logic IC production capacity. From the outset of construction, it is evident that both Japan’s public and private sectors have provided full support, significantly impacting the Kumamoto region. This development has even been referred to as the “semiconductor bubble.” Both Powerchip Semiconductor Manufacturing Corporation and United Microelectronics Corporation are keen on expanding their presence in Japan. In these expansions, Taiwan will contribute its semiconductor manufacturing experience and technology, while Japan will provide the manpower, subsidies, and local resources to increase semiconductor production capacity. This collabortion will also serve as a valuable foundation of experience for Taiwanese companies looking to establish factories in other countries. Furthermore, Taiwan and Japan share some common issues, such as an aging population with a low birthrate, human resource shortages, and the goal of achieving net-zero carbon emissions in the semiconductor supply chain. Other areas, such as digital transformation, automation, and environmental protection, present opportunities for joint exploration and resolution. As a result, Taiwan and Japan can be expected to cooperate more closely in the semiconductor industry in the future.
Taiwan has convenient transportation infrastructure, facilitating prompt technicla support
Taiwan is an international leader in semiconductor processes
Taiwan ranks number one globally in OEM wafer production
Taiwan continues to invest resources in R&D, enabling it to lead global semiconductor technology
Source: InvesTaiwan
Email:[email protected] / Information Window for Key Innovative Industries
Add: 1F., No. 82, Aiguo E. Rd., Zhongzheng Dist., Taipei City 100031 , Taiwan(R.O.C)
Download
Key Innovative Industries in Taiwan - Semiconductor (7.48 MB)
About Us
InvesTaiwan InvesTaiwan Service Center Department of Investment Promotion, MOEA Department of Investment Review, MOEA Contact TaiwanWhy Taiwan
Reasons to Invest Overview Key Industries for Investment Promotion Incentives Important Policies Success Stories